Maximize Efficiency with the Best Steel Cutter Disc for Precision Cutting

Cutting metal with precision and efficiency requires the right tools, and a steel cutter disc is an essential part of the process. But with so many options out there, how do you choose the best one for your needs? From material compatibility to disc size and thickness, there are several factors to consider. In this article, we’ll break it all down to help you make an informed decision and get the most out of your cutting tools.
Key Takeaways
- Always match the cutting disc to the material you're working with to ensure safety and efficiency.
- Choose the right disc size based on your tool and the depth of cut required.
- Thinner discs are great for precise cuts, while thicker ones handle tougher jobs better.
- Using high-performance discs, like those with ceramic grains, can improve cutting speed and reduce wear.
- Proper storage and usage extend the lifespan of your steel cutter disc, saving you money in the long run.
Understanding the Importance of Material Compatibility
Choosing the Right Disc for Metal Cutting
When it comes to cutting metal, not all discs are created equal. The type of metal you're working with—whether it's stainless steel, aluminum, or cast iron—requires a specific cutting disc. Using the correct disc not only ensures a cleaner cut but also extends the life of your tools. For instance, a disc designed for stainless steel will have a different abrasive composition compared to one meant for aluminum, which helps prevent clogging and overheating.
Identifying Discs for Stone and Concrete
Stone and concrete demand their own specialized cutting discs. These discs are typically thicker and embedded with diamond particles to handle the toughness of these materials. If you try using a general-purpose disc on stone, you’ll likely end up with a worn-out tool and a poor cut. Keep an eye out for discs labeled specifically for masonry or concrete to get the job done right.
Safety Risks of Using Incompatible Discs
Using the wrong disc isn’t just inefficient—it’s dangerous. Mismatched discs can break apart during use, leading to serious injuries. Always match the disc to the material and the tool’s specifications. For example, pairing a disc not suited for high-speed tools can cause instability and accidents. Safety should always come first when selecting your cutting equipment.
Material compatibility isn't just a technical detail—it’s the cornerstone of safe and effective cutting practices. Choosing the right disc for the job can save you time, money, and potential injury.
Selecting the Optimal Disc Size for Your Project
Impact of Disc Size on Cutting Depth
When it comes to cutting depth, disc size is the key factor. Larger discs, such as 230mm, can cut deeper into materials, making them ideal for heavy-duty projects like cutting thick metal pipes or concrete slabs. Smaller discs, like 115mm or 125mm, are better for shallower cuts and detailed work. Using the right size disc ensures you achieve the desired cut without compromising safety or efficiency. If you’re working on a project that requires both depth and precision, consider the material thickness and tool capabilities before choosing your disc size.
Balancing Precision and Control with Smaller Discs
Smaller discs offer greater maneuverability and control, which is perfect for intricate tasks. For example, if you’re cutting thin sheet metal or working in tight spaces, a 115mm disc allows for more precision compared to larger options. These smaller discs are also easier to handle, reducing fatigue during extended use. Keep in mind, though, that smaller discs may not be suitable for projects requiring deep cuts. They’re best for tasks where accuracy is more important than cutting depth.
Safety Considerations for Disc Size
Using a disc that matches your power tool’s specifications is non-negotiable for safety. A disc that’s too large can strain the motor and increase the risk of accidents, while a disc that’s too small may lead to inefficient performance. Always check your tool’s manual for the recommended disc size. For example, the CAT 230mm Angle Grinder is designed to handle 230mm discs safely, offering both durability and precision. Matching your disc size to the tool not only enhances performance but also minimizes the risk of instability during operation.
Exploring Disc Thickness for Different Applications
Advantages of Thin Discs for Clean Cuts
Thin cutting discs are your go-to for jobs where precision matters. These discs are lightweight and create less resistance, making them perfect for cutting thin or delicate materials like sheet metal. They deliver a smooth and clean finish, reducing the need for extra polishing or rework. Thin discs also minimize material wastage, which can save you money in the long run. However, they’re not built for heavy-duty tasks and may wear out faster under high stress.
Durability of Thicker Discs for Heavy-Duty Tasks
When you’re dealing with tougher materials like steel bars or thick pipes, thicker discs are the better option. Their robust design adds stability, which helps prevent breakage during demanding jobs. This makes them ideal for prolonged cutting sessions or when working with dense materials. Keep in mind that while they last longer, they may not provide the same level of precision as thinner discs.
Disc Thickness | Best For | Drawbacks |
---|---|---|
Thin (1-2mm) | Clean, precise cuts | Wears out faster, less durable |
Thick (3mm+) | Heavy-duty, long-lasting tasks | Reduced precision, slower cuts |
Matching Disc Thickness to Material Hardness
Choosing the right disc thickness depends on the hardness of the material you’re cutting. For softer materials like aluminum, a thinner disc works well, ensuring smooth cuts without unnecessary strain. For harder materials like stainless steel, a thicker disc offers the durability needed to handle the job without compromising safety. Always check your power tool’s compatibility with the disc thickness to avoid performance issues.
Picking the right disc thickness isn’t just about performance—it’s also about safety. A disc that’s too thin for a tough material can shatter, while one that’s too thick for a light task can strain your tool and slow you down.
For heavy-duty tasks, consider the CAT Abrasive Depressed Thick Cutting Disc (115mm), designed for durability and stability in demanding metal-cutting applications.
Maximizing Efficiency with High-Performance Cutting Wheels
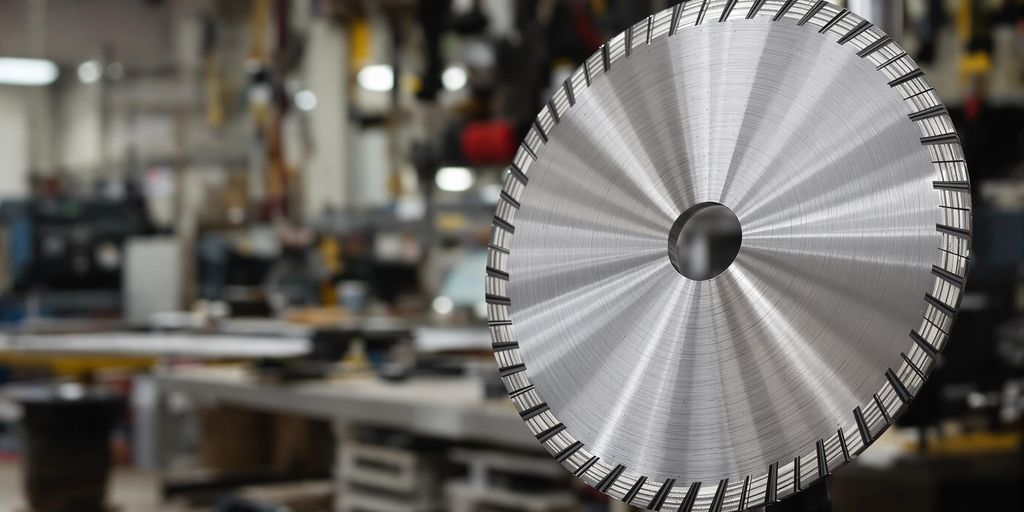
Benefits of Ceramic Grains for Tough Metals
When you’re cutting through tough metals like titanium or armored steel, not all cutting wheels are up to the task. Ceramic grains are a game-changer. These grains are designed to self-sharpen as they wear down, which means you get faster cuts with less effort. Plus, they generate less heat, reducing the risk of material warping or discoloration. The reduced friction also means your tools last longer, saving you money in the long run.
Choosing Thin Wheels for Sheet Metal
For sheet metal, thinner is better. Thin and ultra-thin wheels (like 0.045 inches) cut faster and with more precision because they remove less material. This also means there’s less heat buildup, which keeps your cuts clean and your workpiece looking good. If you’re working on sheet metal, a thin wheel is your best bet for a smooth, efficient cut.
Exploring Abrasive Options for Steel
Steel cutting wheels come in a variety of abrasive materials, each suited for different tasks. For general-purpose steel cutting, aluminum oxide wheels are a solid choice. For tougher jobs, zirconia alumina or ceramic wheels provide extra durability and cutting speed. Matching the abrasive material to your project can make a huge difference in efficiency and final results.
Ensuring Compatibility Between Discs and Power Tools
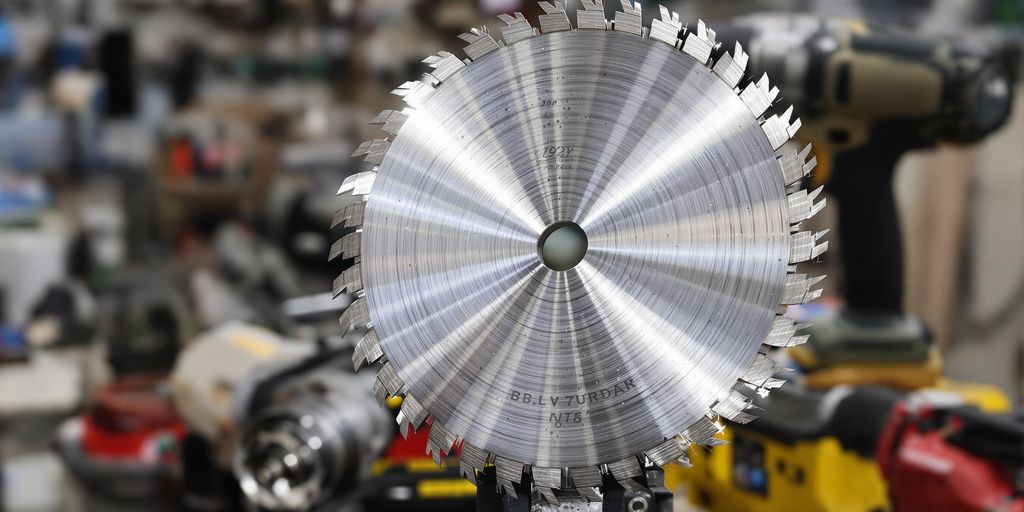
Avoiding Instability with Proper Disc Size
Matching the disc size to your power tool isn’t just about performance—it’s about safety too. Using a disc that’s too large can cause dangerous instability, while a disc that’s too small might not cut deep enough for your project. Always double-check the tool’s manual or label for size recommendations. For example, a tool designed for a 7-inch disc won’t handle a 9-inch disc safely. This simple step can prevent accidents and extend the life of your tool.
Understanding Tool Specifications for Safety
Every power tool comes with a set of specifications, like maximum RPM (revolutions per minute) or arbor size. These details are critical when choosing a disc. A disc with a lower RPM rating than your tool’s maximum speed can shatter, posing serious risks. Likewise, an incorrect arbor size can lead to wobbling or poor performance. Keep these specs in mind to ensure smooth, safe operation.
Specification | Why It Matters |
---|---|
RPM Rating | Prevents disc shattering at high speeds |
Arbor Size | Ensures stable and secure disc attachment |
Material Compatibility | Avoids inefficient cuts and tool damage |
Enhancing Accuracy with Compatible Discs
When your disc and tool work well together, your cuts are cleaner and more precise. A compatible setup minimizes vibrations, giving you better control and reducing wear on both the disc and the tool. If you’re working on metal sheets, for instance, a circular saw like the Kress 185mm with an appropriate disc can make all the difference in achieving accurate cuts. Precision isn’t just about skill—it starts with the right equipment.
Taking the time to match your disc to your tool isn’t just about getting the job done; it’s about doing it right and staying safe while you’re at it.
Best Practices for Prolonging Disc Lifespan
Proper Storage to Prevent Warping
How you store your cutting discs can make or break their longevity. Keep them in a cool, dry place, away from direct sunlight or extreme temperatures. Moisture and heat can cause warping, which makes the disc unsafe to use. If you’re storing multiple discs, use a vertical rack or a flat, padded surface to avoid bending or pressure damage.
Minimizing Wear Through Correct Usage
Using your cutting disc properly is just as important as storing it right. Avoid applying excessive pressure while cutting; let the tool do the work. Overloading the disc can cause it to wear out faster or even break. Always match the disc to the material you’re cutting—using a disc designed for steel on concrete, for example, will lead to rapid degradation.
Pro Tip: Check the RPM rating of your disc and ensure it matches your tool’s speed to avoid unnecessary wear.
Balancing Cost and Quality for Longevity
It’s tempting to go for the cheapest option, but budget discs often wear out quickly, costing you more in the long run. Invest in high-quality discs that are designed for durability. While the upfront cost is higher, you’ll save on replacements and get better performance.
Disc Type | Average Lifespan | Cost-Effectiveness |
---|---|---|
Budget Discs | Short | Low |
High-Quality Discs | Long | High |
A good-quality disc not only lasts longer but also ensures safer and more efficient cutting, making it a smarter choice for frequent users.
By storing your discs properly, using them as intended, and prioritizing quality over short-term savings, you can significantly extend their lifespan and get the most value out of your investment. For example, the Kress 115mm, 900W Angle Grinder is compatible with a range of high-performance discs, ensuring both durability and precision in your tasks.
Leveraging Power Tools for Precision Metal Cutting
Advantages of Ergonomic Designs
A good ergonomic design can make or break your experience with a power tool. Tools with comfortable grips and well-balanced weight distribution reduce hand fatigue and strain, especially during long projects. Ergonomic power tools not only improve comfort but also boost accuracy, as you maintain better control over the cutting process. Look for features like anti-vibration handles or adjustable grips to suit your needs.
Safety Features for Risk Reduction
When working with metal, safety should be your top priority. Modern power tools often come equipped with features like blade guards, emergency stop buttons, and automatic shutoff systems. These additions minimize risks and help you focus on the task at hand. Always double-check that your tool's safety mechanisms are in working order before starting a project.
Versatility in Metal Cutting Applications
Power tools can handle a wide variety of tasks, from cutting thick steel beams to shaping delicate metal pieces. For instance, the CAT 18V Mini Cordless Circular Saw is ideal for precision cuts in both heavy-duty and fine-detail jobs. With adjustable speeds and interchangeable blades, you can adapt a single tool to multiple applications, saving both time and money.
Power tools have revolutionized metalworking, offering unmatched precision, speed, and safety. Whether you're a seasoned pro or just starting out, investing in the right tools can transform your projects.
Using power tools can make metal cutting much easier and more accurate. These tools help you get clean cuts without much effort. If you're looking to improve your metal cutting skills, check out our selection of power tools. Visit our website to find the right tools for your projects!
Conclusion
Finding the right steel cutter disc can make all the difference in your projects. It’s not just about getting the job done; it’s about doing it safely, efficiently, and with precision. By considering the material, disc size, thickness, and compatibility with your tool, you can save time, reduce wear on your equipment, and achieve cleaner cuts. Remember, investing in a quality disc upfront often pays off in the long run by delivering better results and lasting longer. So, whether you’re tackling a big project or just need a quick fix, take the time to choose the right disc—it’s worth it.
Frequently Asked Questions
What materials can I cut with steel cutter discs?
Steel cutter discs are designed for cutting metals like steel and aluminum, but some are also suitable for stone or concrete. Always check the label for compatibility.
How do I choose the right disc size for my project?
The disc size depends on your tool and the depth of cut you need. Larger discs cut deeper, while smaller ones offer better control for detailed work.
What’s the difference between thin and thick cutting discs?
Thin discs are great for clean, precise cuts, while thicker discs are more durable and better for heavy-duty tasks. Match the disc thickness to the material you're cutting.
Can I use any cutting disc with my power tool?
No, you must use a disc that matches your tool’s specifications. Using the wrong size or type can cause instability and safety risks.
How can I make my cutting discs last longer?
Store them in a cool, dry place and avoid applying too much pressure during use. Proper usage and storage help extend their lifespan.
Are there special discs for cutting tough metals?
Yes, discs with ceramic grains or specific designs are ideal for cutting hard metals like titanium or stainless steel. These discs reduce heat and wear for better performance.